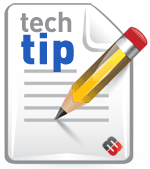
Epoxy resins are widely used as insulation material in electrical and electronic applications. They are employed as adhesives, sealants, coatings, impregnants, moldings and potting compounds to produce void-free insulation around components. The selection of a specific epoxy formulation for a given application requires not only an understanding of desirable dielectric properties, but also many other characteristics such as physical and mechanical strength, chemical resistance, operating temperature range and thermal cycling, dimensional stability and resistance to shock and vibration.
Epoxy resins for electrical and electronic applications can be divided into two general categories: epoxies with amine type curing agents and those coupled with anhydride curing systems. Epoxy resin systems that contain amine are most frequently employed as adhesives, sealants, impregnants and coatings. Anhydride epoxy compounds are primarily employed for encapsulation and potting purposes, especially for applications which have high temperature demands or large volume usage.
The high speed offered by UV curable epoxy formulations has increased their popularity in high performance bonding, sealing and coating applications. Master Bond offers UV curable compounds that can cure at ambient temperatures, in the presence of oxygen, in less than one minute.
The chart below summarizes some of the most important characteristics in evaluating the electrical performance of epoxies:
Dielectric Properties of Epoxy Insulation Materials
- Volume Resistivity
- The measurement of the ability of an insulating material to resist the passage of electric current through the thickness of a solid specimen under specified conditions. A typical unfilled epoxy has a volume resistivity of >1010 ohm-cm at 25°C.
- Surface Resistivity
- The measurement of the ability of an insulating material to resist the passage of electrical current along the surface of a solid specimen under specified conditioning. A typical unfilled epoxy has a surface resistivity of >1010 ohm-cm at 25°C.
- Dielectric Constant
- The measurement of the strength of a given specimen at a specified thickness and is expressed in volts/mil. Dielectric strength decreases with specimen thickness. Typical values for epoxy specimen 0.125 inches thick are in the 420-480 volts/mil range.
- Arc Resistance
- The measurement of the resistance to a specified high voltage, low current arc conditions in terms of seconds to insulator breakdown. Values for typical epoxies are in the 100-300 second range.
- Dissipation Factor
- The measurement of the energy lost to the dielectric material in an alternating field.
ASTM test methods are generally used for measuring these values. The table below lists the various properties and the corresponding test used for measurement.
Electrical/Electronic Test Methods for Epoxy Resins | |
---|---|
Property | Test Method |
Volume Resistivity | ASTM D257 |
Surface Resistivity | ASTM D257 |
Dielectric Constant | ASTM D150 |
Dielectric Strength | ASTM D149 |
Arc Resistance | ASTM D495 |
Dissipation Factor | ASTM D150 |
All of the properties listed, are affected to some degree by temperature and the addition of inorganic fillers such as silica, alumina and glass. For this reason, designers tend to use the highest values for volume and surface resistivity, dielectric strength and arc resistance, and the lowest values for dielectric constant and dissipation factor.
Master Bond offers epoxy compounds for every type of electrical insulation application. They include both amine and anhydride curing compositions as well as an innovative line of UV curing products. The product line includes compounds for service from cryogenic temperatures to as high as 600°F including NASA low outgassing certified systems. Two particularly noteworthy Master Bond products are EP30-2, an optically clear, low viscosity epoxy system with a volume resistivity as high as 1016 ohm-cm which meets NASA’s stringent low outgassing requirements for aerospace use, and EP112, a very low viscosity cycloaliphatic epoxy system with superior arc resistance for use up to 500°F. Master Bond’s technical support team would be glad to recommend a product that meets your particular application’s requirements.