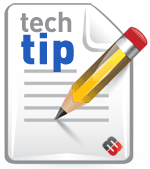
On the most basic level fungal build up on epoxy resin systems weaken the core performance properties of the adhesive itself resulting in adhesive failure. The fungus work to break down the resin into smaller particles as a nutritional source to obtain carbon. Among other things, this degradation causes the adhesive, sealant or encapsulant to lose its ability to protect against chemical and moisture exposure. Below is an outline of the harmful effects of fungus on epoxies:
Material Deterioration
The physical properties of the adhesive are compromised due to the molecular degradation caused by the fungus.
Electrical Failures
At times the fungal growth can create an electrical bridge over insulating materials producing electrical failures.
Restricted Movement of Small Parts
The fungus can fuse together small mechanical parts restricting their movement.
Moisture to Non-Wetting Surfaces
Fungal communities introduce moisture into their living environments which can cause further damage to bonded parts.
How do fungus resistant adhesives work?
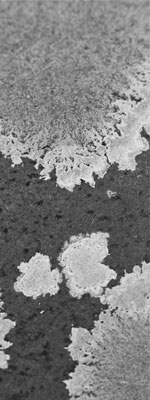
How do you test an adhesive’s fungus resistance?
One of the most robust ways of testing adhesives for fungus resistance is with the MIL-STD-810G with Change 1, Method 508.7 standard. This stringent military standard was developed by the U.S. Department of Defense. It is used to determine the extent to which a product will support fungal growth, how that growth can affect the performance of the material, and what specific species have grown. The epoxy samples are inoculated with a spore suspension consisting of the following organisms:
- Aspergillus flavus
- Aspergillus versicolor
- Penicillium funiculosum
- Chaetomium globosum
- Aspergillus brasiliensis (formerly known as A.niger)
How is the MIL-STD-810G standard test performed?
MIL-STD-810G with Change 1, Method 508.7 was employed on many Master Bond products to determine their fungus resistance. Products were rated for amount of growth with 0 being devoid of microbial growth and 4 representing massive growth.
Fungus Rating Guideline | ||
---|---|---|
Growth Amount | Rating | Observation |
None | 0 | Substrate is devoid of microbial growth |
Trace | 1 | Substrate is devoid of microbial growth. |
Light | 2 | Intermittent infestations or loosely spread microbial colonies on substrate surface. |
Medium | 3 | Substantial amount of microbial growth. Substrate may exhibit visible structural change. |
Heavy | 4 | Massive microbial growth. |
Specimens were preconditioned at 30°C and 90% minimum relative humidity within the test chamber. They were then sprayed with prepared spore suspension. The objective was to assess the select adhesive system to ascertain if it would support fungus growth, whether it can function after exposure and identify the species (if growth occurs). Samples were tested for 28 days and exhibited no signs of fungal growth. Specified temperature for test and moisture level was most conducive for spore germination and growth. Sample specimens were compared with a control sample. Below are a handful of the tested epoxies including their test results:
Test Results of Master Bond Fungus Resistant Systems | ||
---|---|---|
Part Number | Product Information | Visual Results After 28 Days |
MasterSil 151AO | Flexible silicone casting, potting and sealing system with thermal conductivity of 0.35-.0.54 W/(m•K) | 0 – None |
EP36AN | B-stage epoxy potting & bonding compound with outstanding toughness and resistance up to 500°F | 0 – None |
EP39MAOHT | Low viscosity epoxy with superior dielectric properties resists thermal cycling and mechanical shock | 0 – None |
EP3RR-80 | One part epoxy cures at 80°C or higher features low exotherm upon cure | 0 – None |
EP30LTE-LO | Two part epoxy with extra low coefficient of thermal expansion and unmatched dimensional stability | 0 – None |
EP37-3FLFAO | Flexible, low viscosity, thermally conductive epoxy meets NASA low outgassing specifications | 0 – None |
Control Specimen | Consists of sterile potato dextrose agar and unbleached, plain weave, 100% cotton cloth strips | 4 - Heavy growth (60% to complete coverage) |
Learn more about our systems meeting MIL-STD-810G specifications